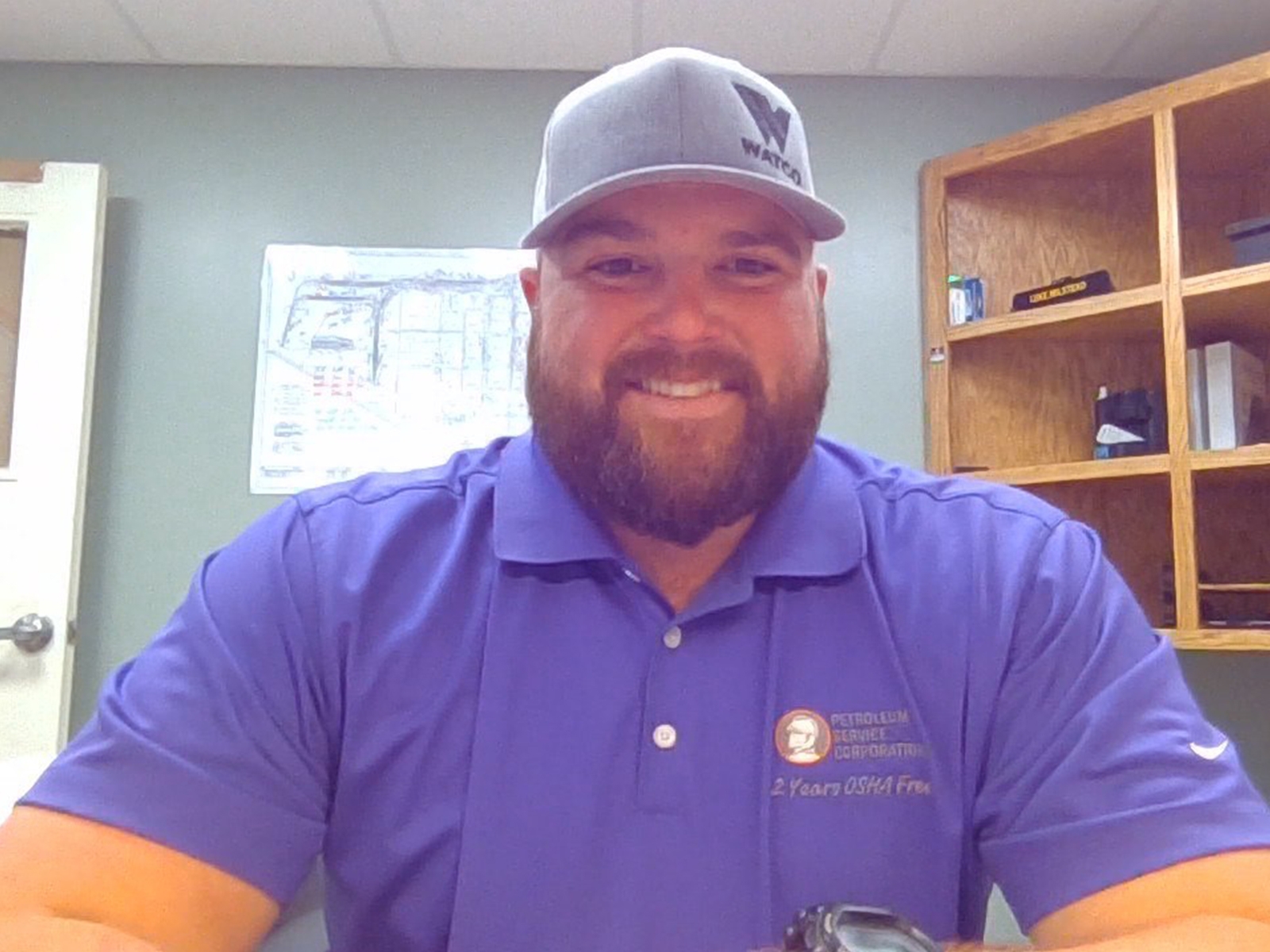
Quick Response Prevents Costly Losses
November 2021 – A service interruption at any industrial facility can result in a loss of productivity, a loss of income or added expenses, and additional negative repercussions. When a customer ran into an unplanned outage at a Louisiana location, Watco team member Luke Milstead managed a quick response that prevented any costly losses.
An industrial facility where Watco handles a customer’s rail-based transportation had an issue and was unable to produce a chemical required to run their plant. This location put the word out that they needed a special train containing 10 loaded tank cars of the needed chemical. Milstead, Manager of Train & Rail Operations at a sister plant nearby, answered the call.
The same day the first plant issued its request, Milstead and his team at the second plant made provisions to get 10 tank cars to the rack, and then put those together with the buffer cars that are required between the locomotive and tank cars.
“Luke was driving this and came up with the strategies that made it possible, along with a couple of contract providers that executed Luke’s plan,” said his Site Manager Russell Spragis. Milstead came up with a switching strategy that allowed lining up the tank cars, getting them to the facility and loaded, and pulling them out of the facility and onto the outbound track in position for a Union Pacific Railroad team to come into the plant for the train.
And he managed to assist the first plant without causing any delays at his own location. “He still kept our operations on schedule,” said Spragis. “He kept our normal operations on time and flowing as needed.”
Read about others like Luke who are making a difference at Watco and beyond. Learn More