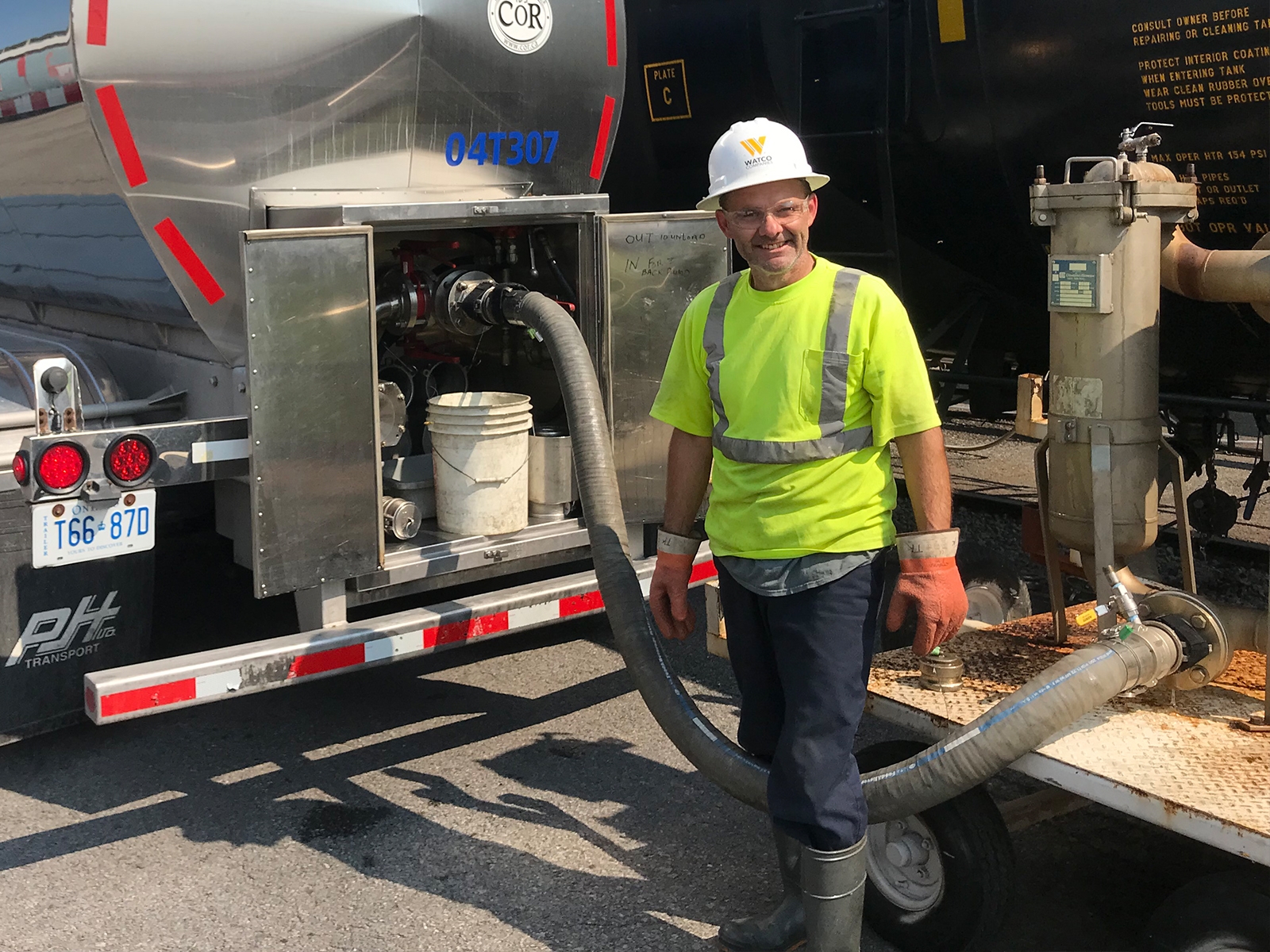
Loader’s Keen Eye Halts an Incorrect Shipment
December 2021 – Thanks to Tom Kaczynski’s eye for detail, Watco saved a customer from shipping 60,000 pounds of the wrong product and possibly contaminating their end customer’s silo.
Kaczynski is a Loader for the Buffalo Transload Terminal (TBT) in New York, which Watco operates for Norfolk Southern Railway. Although he eyeballs samples of syrup routinely as part of his job, he remains attentive, and on one shift he noticed something he didn’t like during his inspection. Although corn syrup varieties come in many shades, as Tom held a transparent container up to the sunlight, its contents looked too watery to him.
“Every load we take, the customers require a sample to go with the load so they can test as well,” says Terminal Manager Shawn MacWilliams. “We hold it up to the sun and make sure there’s no debris in it, make sure the color is clear. Tom took the sample, and it was really watery and should’ve been thick. He immediately stopped the load and brought it to my attention.”
Kaczynski’s instincts about the syrup’s consistency were correct. The “solids content” – one of the many properties of corn syrup – wasn’t right. “We have a refractometer to test the dry solids,” says MacWilliams, “and when we did that, the dry solids come out wrong. We have four different grades of corn syrup, and the dry solids are different for all of them. We took the sample and tested the dry solids, which came back out of spec.” It turned out that the sample contained 10 percent less dry solids than it should have, according to the certificate of analysis (COA) that came with the load, which lists the percentages of ingredients, among other things “That’s how we know what’s supposed to be in that railcar.”
MacWilliams contacted the customer. “They did their research, and someone had sent a reprocessed, different product. “It turns out they sent us a wrong COA with the railcar, and it was the wrong product.”
Kaczinski’s catch saved the Watco customer from sending the wrong product to their customer, which likely would’ve ended up in a silo, contaminating the original contents. That would mean the costly effort of draining, cleaning, and refilling the silo.
Our customer conveyed their thanks for Kaczinski’s thorough, attentive approach and a catch that likely saved them a lot of money. “Tom never cuts corners,” says MacWilliams. “He does his due diligence all the time. He’s always on top of stuff. He’s actually perfect for this job.”
Read about others like Tom who are making a difference at Watco and beyond. Learn More